Understanding the Basics of Welding Inspection to Ensure Quality and Safety
In the world of modern engineering, welding inspection stands as a foundation for ensuring both the top quality and security of architectural developments. What are the subtleties of these evaluation methods that make them vital for maintaining structural integrity?
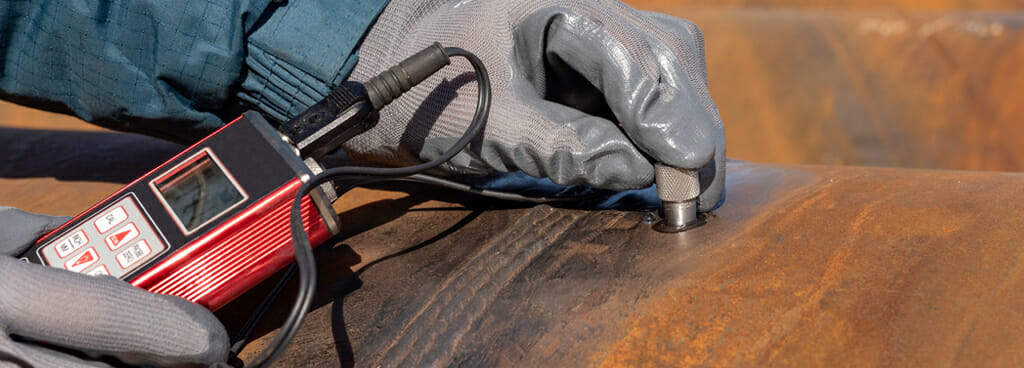
Importance of Welding Assessment
In the world of industrial fabrication, the significance of welding examination can not be overemphasized. Welding inspection plays a crucial function in making sure the honesty, safety and security, and longevity of welded frameworks. Offered the varied applications of welding in sectors such as building and construction, automotive, aerospace, and shipbuilding, the need for stringent quality control steps is vital. Correct inspection guarantees that welds fulfill specified requirements and codes, which is necessary for avoiding structural failings that might result in devastating effects.
The procedure of welding naturally involves complex variables, including temperature, product properties, and ecological conditions, every one of which can affect the quality of the weld. A detailed inspection recognizes issues such as splits, porosity, and incomplete blend, which can jeopardize the stamina and integrity of the weld. By identifying these problems early, corrective actions can be taken, thereby lowering the danger of failure and associated expenses.
In addition, welding examination contributes to governing compliance, as several sectors are controlled by stringent safety requirements and standards. Failure to stick to these regulations can result in legal liabilities and economic fines. Ultimately, welding assessment not only safeguards physical structures but also upholds and secures human lives market credibilities.

Key Welding Assessment Techniques
Although welding evaluation is crucial to guaranteeing the quality and security of welded frameworks, it is the certain methods employed that figure out the performance of the assessment procedure. Secret welding assessment approaches can be extensively classified into non-destructive screening (NDT) and damaging screening.
Radiographic and ultrasonic screening are advanced methods that allow examiners to examine the inner honesty of the weld. Ultrasonic screening makes use of high-frequency audio waves to discover discontinuities, while radiographic testing utilizes X-rays or gamma rays to generate an image of the weld's inside. Magnetic bit testing and liquid penetrant screening are surface area evaluation approaches made use of to find surface area and near-surface problems. On the other hand, destructive testing methods involve literally reducing the weld or breaking to analyze its mechanical buildings. These thorough evaluation methods make certain that welds fulfill sector requirements and security demands, therefore making sure structural honesty and performance.
Duty of Qualified Inspectors
Certified inspectors play an essential function in the welding examination process, making certain that all welds abide by strict industry requirements and security regulations. Their expertise is vital in determining flaws or abnormalities that may endanger the structural integrity of a weld. By diligently examining each weld, certified examiners assist stop potential failings that can bring about harmful mishaps or expensive repair services.
To end up being licensed, examiners must undertake extensive training and screening, which acquaints them with different welding strategies, products, and screening approaches. This comprehensive knowledge permits them to review weld high quality successfully and make informed judgments about their safety and dependability. Qualified assessors are competent in analyzing specs and blueprints, making certain that the welding work lines up with the project's style demands.
An important component of their function is to record their findings extensively, offering a thorough document of the examination process. Their payment is essential in keeping high levels of high quality and safety in welding operations.

Devices Utilized in Welding Inspection
Welding assessors depend on a range of specialized devices to perform their responsibilities effectively, ensuring each weld satisfies the necessary requirements. Amongst these devices, visual assessment aids like magnifying glasses and mirrors are fundamental, allowing examiners to closely examine welds for surface area flaws such as cracks, porosity, and undercut. Calipers and fillet weld evaluates are vital for measuring weld dimensions to verify compliance with design specs.
Advanced tools extend past visual aids, consisting of non-destructive testing (NDT) devices. Ultrasonic screening tools are pivotal in finding subsurface imperfections, utilizing sound waves to disclose inner interruptions without compromising the weld's integrity. In a similar click for info way, radiographic screening utilizes X-rays or gamma rays to capture photos of a weld's interior, highlighting prospective defects.
Magnetic find more information fragment testing is one more crucial device, specifically for detecting surface and near-surface discontinuities in ferromagnetic products. By applying ferrous fragments and magnetic areas, inspectors can identify problems that could otherwise be unseen.
Dye penetrant inspection is frequently utilized for non-ferrous products, providing a contrast-enhanced visual look for surface-breaking flaws. Welding Inspection Madison. Together, these tools allow welding assessors to thoroughly assess weld high quality, guaranteeing safety and security and dependability in different applications across sectors
Making Sure Architectural Honesty
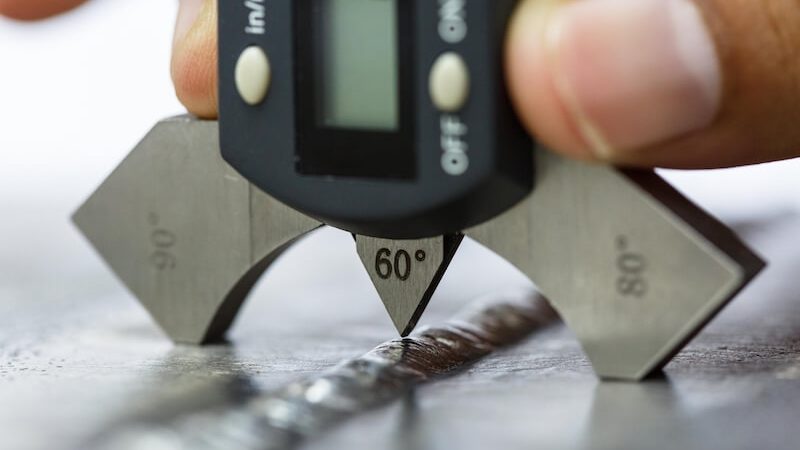
Welding treatments should follow well-known criteria and codes, such as view website those defined by the American Welding Society (AWS) or the International Company for Standardization (ISO) These guidelines guarantee that the welds can stand up to functional stresses and environmental aspects. Certified and licensed welders play an important role in this process, as their competence guarantees that methods are applied correctly, minimizing problems such as cracks, porosity, and insufficient combination.
Post-weld evaluation is one more crucial element of confirming structural integrity. Non-destructive testing (NDT) methods, including ultrasonic testing and radiographic testing, are utilized to identify subsurface imperfections without endangering the bonded framework. These evaluations validate that the welds fulfill the required top quality requirements, giving assurance of their durability and integrity. Ultimately, guaranteeing architectural integrity in welding not only safeguards human lives but additionally safeguards financial investments and enhances the long life of engineered frameworks.
Verdict
The basics of welding examination are essential for preserving the quality and safety and security of bonded structures. The usage of specialized tools further improves the evaluation procedure, ultimately securing human lives and prolonging the lifespan of bonded constructions.
Welding inspection plays a crucial duty in making certain the integrity, safety, and durability of welded structures.Although welding inspection is important to making certain the high quality and safety of welded frameworks, it is the certain methods used that identify the effectiveness of the evaluation process. Key welding examination techniques can be generally categorized into non-destructive screening (NDT) and destructive testing.Certified examiners play a pivotal duty in the welding inspection process, making sure that all welds abide with strict market standards and safety and security laws.The basics of welding inspection are vital for maintaining the quality and safety of bonded structures.